Badminton Shuttlecock Deep Dive - Comparing Materials Of 20 Different Shuttles (Cork, Feather, Glue & Thread)
- CKYew
- Feb 5
- 10 min read
The badminton shuttlecock is such an underrated consumable that we rely heavily on having a good game of badminton. I’ve gone through 20 different shuttles from multiple models and brands, and we’re going to take a closer look at the construction of this incredible thing, especially around the cork area. That area is fascinating!

There is so much to unpack here and it feels like I'm continually discovering something new and more questions come up. But here is everything I've learnt so far, and spoiler alert, I found a literal screw inside the cork of a shuttle! Keep reading to find out more!
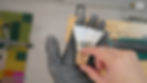
Firstly, this mini-project would not have been possible without RSL’s help. RSL is one of the biggest shuttle manufacturers in the world, and a true expert there gave me a lot of his time explaining many of the questions I had alongside the necessary context and background info. I was told that RSL currently produces around 1-1.2 million tubes of shuttles a month, which is almost 15 million shuttles a month, so they know the production of a badminton shuttlecock very well. So, a big thank you to them, and watch out for an upcoming piece where I put their shuttles through their paces via a structured testing regime before comparing their performance!

In very simple terms, a badminton shuttlecock, birdie, shuttle, or ball, however you want to call it, weighs around 5 grams and has 16 feathers. It generally consists of only four components and six materials. The four components are split into the feather, the cork, the string, and the glue. The cork is then further divided into the leather outside the cork and the tape around it to help us easily identify the shuttle during flight.
Badminton Shuttlecock Cork Designs
Let’s start with the cork. I have already cut a few shuttles open before, so I knew certain manufacturers did multilayered cork bases for shuttles. This time, I thought I would get serious and hook up a jigsaw and slice them all open because the last time, I used a Stanley knife and pen knife, and that didn’t go too well.
However, a few shuttles in, I had a big surprise when my jigsaw jumped whilst cutting through the cork, and I didn’t realise it at first because it was loud, but I picked up a screw off the floor, and I was like WHAT??!!

As I was filming the cutting process, I rolled back the footage and saw the screw come out of the Chao Pai Purple shuttle. I’ve never known screws were placed into corks to make sure they have the right weight so this was a new finding! However, the other 19 shuttles I cut up didn’t have any screws, but I did have one shuttle that didn't even have a cork. It was a super low-end shuttle from the 361 brand which was part of my recent Temu badminton equipment review.
The super low-end shuttle didn’t even have a cork base, and it was all foam, which explains why the shuttle felt spongy and erratic as once the foam deforms, it doesn’t bounce back and regain its shape. So if you cut one of your shuttles open and it’s foam, it's not a good sign!
However, once I had gone through all the cutting, I quickly realised manufacturers use very different techniques and materials in production, depending on the price point of the shuttle. Almost all brands have some form of multilayered cork. Higher-end shuttles tend to have 2 layers of cork base, and 3 layer cork bases are also present in premium and standard-range shuttles.
Additionally, what was interesting to see was how manufacturers employ different cork base designs to produce excellent shuttles. Here I have some of the best shuttles on the planet and this is the Yonex AS50 shuttle (UK here) as well as the Yonex F-90 Tournament shuttle, which are used at the Olympics, World Championships, Japan Open and the All England:
And here is the Victor Master Ace, Victor’s highest-end premium shuttle:
And Li Ning’s G800:
Lastly, these are RSL’s high-end options, the Tourney Classic and Tourney Number 1 shuttles. All of these shown here are BWF-certified high-end premium shuttles.
Have you spotted any difference in the cork layout from all these shuttles yet?
You can see that the Yonex shuttles employ a 2 layer cork base design where a small piece is very close to the head of the cork base whilst in Victor and Li Ning’s shuttles, the Victor Master Ace has a 50:50 split cork design, whilst the Li Ning has the opposite configuration to the Yonex shuttles. The RSL’s have a different design where the layer of natural cork which is closer to the head is made from finely crushed natural cork before they are compressed and glued together whilst the top layer is a type of synthetic cork. So very different manufacturing designs and processes there.
So why use natural cork?
It’s all down to the ability to absorb and transfer the energy coming from our racket and strings and being able to bounce back into shape after impact. The cork’s signature feeling is quite key to how a shuttle feels as our strings tend to contact the head of the cork first so that’s why shuttles have natural cork around the head area. Natural cork in bigger pieces also costs more too so hence they’re generally found in more premium shuttles.
Additionally, natural cork is an organic material hence it will naturally have holes and gaps as it’s part of a tree. As shuttle manufacturers try to engineer very precise shuttles with very fine tolerances, it gets challenging to have big pieces of cork cut to specific specifications as it’s a natural product. Hence, RSL’s designs allow them to accurately and finely control their cork bases’ specifications and production process. Both methods have pros and cons, but what is fantastic is that manufacturers use different methods to solve this design challenge.
Also, synthetic corks are generally softer than natural corks. Hence, they are often found in the middle or upper layer of a shuttle’s cork base where the feather stems are inserted.
Here are some shuttles with a 3-layer design like Yehlex’s, which is a popular brand in the UK. The Yehlex shuttles I’m testing here are from their top 3 grades available. We’ll call them yellow, orange and purple because of their sticker colour.
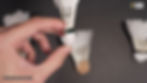
We can see here that natural cork is present on the head of the cork base, whilst the middle layer is a synthetic cork, and the small layer at the top is synthetic or natural cork, depending on the grade of the shuttle. The downside of having multilayered cork bases is sometimes you’ll see there are bulges around the cork area where the glue connecting the cork layers has worn out, and a layer of either synthetic or natural cork has swelled, causing that ring which we see around the leather.

I’ve also noticed that higher-end shuttles have their feather stems inserted at a deeper level around 13-15mm whilst less premium ones go up to 12mm. In summary, plenty of configurations exist for a shuttle’s cork base, depending on the brand and which model shuttle you play with. Generally, the more premium a shuttle is, the bigger the single piece of natural cork inside it. Crushed natural corks are a smart solution to ensure consistent quality control during production.

The Chao Pai shuttles that I’ve got here are about 10 years old, and I think inserting screws into them is a pretty old method of ensuring the shuttle makes the required weight. Also here is a microscope view of the cork, it’s pretty interesting.
Remember to protect your precious badminton rackets from chips and scratches with the Premium Racket Protection Tape with free delivery worldwide on ckyew.com/shop. We also have some super limited edition player signed prints too!
Badminton Shuttlecock Feather Designs

If we then look at the feather of a shuttle, many of us know badminton shuttlecocks use two types of feathers, goose and duck. As far as I’m aware, duck feathers are commonly referred to as the less premium feather when compared to goose feathers. However, we must also remember that there are levels to this and it is important to note if we compare high-end goose feathers to high-end duck feathers, the goose will probably be better, but the margins are very close. The mid-range goose feathers will actually lose out to high-end duck feathers. As a matter of fact, I personally am not able to tell if a shuttle is made from goose feathers or duck feathers just from visual inspection, but I have recently been pleasantly surprised to find out some of the shuttles which I have rated highly are actually duck feathers! Very interesting there.
Generally in Europe, shuttles tend to be on the higher-end spectrum due to the buying power and expectation of quality. Hence, many of the 20 shuttles I’ve sliced up here are considered pretty high-end shuttles. There are different feather types, some with a fuller shape, and others less.
Modern shuttlecock factories are highly automated and manufacturers buy feathers in bulk from farmers. However, sorting them is a huge challenge to ensure quality and consistency in production. Brands generally separate feathers into categories such as left wing, right wing, colours, whiteness, angle of the feathers, bird type etc. My shuttle expert tells me RSL’s factories are sorting the raw feathers they get from farmers into 50,000 different feather categories, depending on the parameters they need! Yep, 50 thousand - I even had to double check!
That’s only possible because of the sheer amount of shuttles they process. 1.2 million tubes of shuttles is 14.4 million shuttles which requires over 230 million pieces of feathers. A month! These 230 million feathers have passed quality control and are used for production. Imagine the raw numbers. You get the idea. So 50,000 different types of feather configurations is probably correct for the quantity of feathers passing through the production floor.
In high-end shuttles, only feathers from the same exact spec like the same wing, same feather, size, shape, angle, etc are combined together before they are punched into the cork. I was also told that in the earlier days, manufacturers tended to bleach their feathers so they looked cleaner and brighter white. However, I’m aware that brands such as RSL don’t bleach theirs anymore as they believe it damages the feathers, and so the only bleaching comes from their drying process, when they lay the feathers out to dry in the sun after the washing process.
From the shuttles I’ve sliced up here, many of them are used shuttles but the new ones are indeed punched out to perfection and the stem is stiff and crisp. The tips with the feathers are pliable and can store lots of energy before flicking back when released.
Higher-end shuttles tend to have full feathers and lower-end shuttles have partial feathers with various degrees of slight damage as we go down the quality chain.
If we zoom in on them on the microscope, we can also see some incredible detail, even down to the individual strands of little hairs on the end of each feather. When we use a different type of microscope, a scanning electron microscope, we’re actually able to zoom in individually on the feathers and at just 100 times magnification, we’re even able to see the cell structure on the individual strands of feather. Incredible!
As I was going through my scanning of the feathers, which I cut out from ready-made shuttles, you could also see the glue and string that had tied the shuttle together. It's pretty impressive that the microscope is able to show so much detail.
Next up from the feathers is the thread and glue. In terms of threads, the only difference I can tell from the low-end to the high-end shuttles is the thickness of the threads used.
Additionally, it looks like the nicer shuttles are all machine-sewn, whilst the low-end shuttle looked like it was hand-tied. The threads look similar, but all mid-range to high-end shuttles have the threads glued to provide structural stiffness, whilst the super low-end shuttle isn’t even glued.
My shuttle expert told me glue is the secret sauce to shuttle making. In his opinion, if everything is equal, it’s the glue that’s the superstar and the ingredient that makes a difference. Apparently, it’s a complete science to determine what glue to use and each manufacturer has their proprietary secret glue mix for their shuttles and I’ve also been told that the glue used for shuttles designated for different regions differ in its properties.
For example, shuttles destined for humid areas all year round have slightly less moisture content. In comparison, shuttles destined for the European markets have a glue blend that has a slightly higher moisture content as the conditions in Europe are drier, especially in winter compared to say, South East Asia.
Badminton Shuttlecock Quality Maintenance
Manufacturers like RSL will also try to keep their shuttles as fresh as possible by adding a little bit of moisture into their tubes of shuttles before sealing them for transportation. Depending on where you are, transportation from the factory to the final retail location may take months. Hence it is important to keep the freshly produced shuttles in their best condition for as long as possible.
Obviously, I also asked what would be the optimum shelf life for a shuttle that’s been produced, and the answer I got is around 24 months. This doesn't mean that shuttles over 2 years old are not fit to play with anymore. Speak to the retailers you buy your shuttles from and they will be able to tell you how fresh the shuttles are.
Generally, I believe we’re still in quite a big shuttle shortage all around the world. Depending on what brand you normally play with, I don't think many retailers are storing their shuttles long on the shelf. One key thing about ensuring shuttles are performing at their best is storing them correctly. I was told that clubs in Denmark are storing their shuttles in temperature and humidity-controlled enclosures and they were able to save costs on their annual shuttle spend as the shuttles were performing at their best all the time.
RSL also said they’ve tested at the Badminton Europe Centre of Excellence and found the optimum humidity for shuttles to be at 86% relative humidity. Temperature-wise, around 18-21 Degrees Celsius would be best but obviously if you’re in warmer or colder climates, just make sure your shuttles are not experiencing big temperature fluctuations.
Finally, if you do find your shuttles a little bit too dry and brittle, you can simply re-steam them which you can learn how to do here. Be careful not to overdo it though!
I hope you’ve learnt something new about the shuttles that we play with! Put any questions you have in the comments and hopefully I’ll be able to visit a shuttle factory and continue with a part 2. I’ll see you in the next one!